Highly engineered medical device solutions for your medical innovations
Vaupell is a leading medical device solutions partner for highly engineered, injection molded advanced plastic components and assemblies for medical product OEMs. Products include a wide variety of plastic and metal components and assemblies used in medical products such as:
-
- Surgical tools & instruments
- Implantables & bioabsorbables
- Drug delivery
- Orthopedics
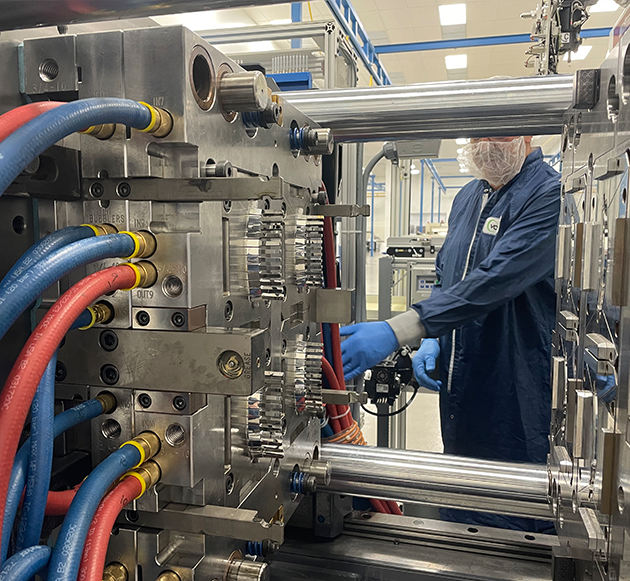
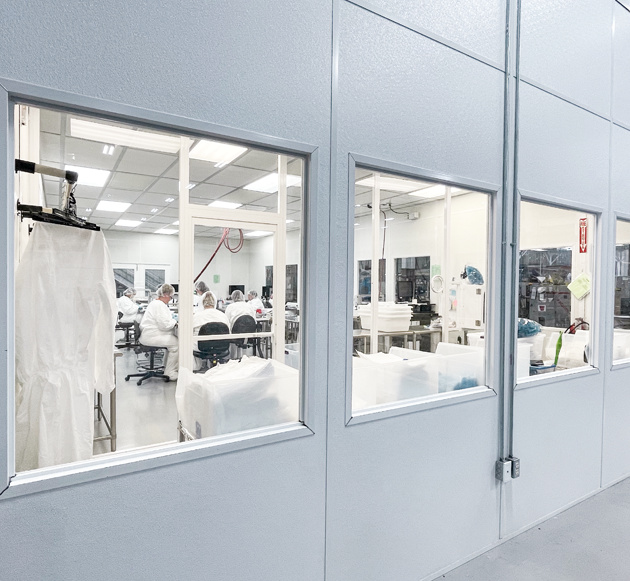
Precision and focus in all we do!
The rigorous technical requirements of medical devices, make the medical market a strong fit with Vaupell given its engineering capabilities. Commonly used materials in molding medical devices and equipment includes Acetals, Nylons, Polysulfones, PEEK, PEKK and Ryton®, for which Vaupell is considered a leader in molding.
Our capabilities include: Program management & engineering support, Design & development, In-house tooling, Mold building, Precision machining, Injection molding, Automation, Assembly & packaging, and Cleanroom manufacturing.
Certifications: FDA , ISO, & MedAccred Accredited.
The markets we serves: Your medical device solutions partner
Vaupell—A full product life-cycle partner. We’re your global medical device solutions partner for highly engineered Implantables & bioabsorables, Surgical tools & Instruments, Drug delivery, and Orthopedic medical devices & assemblies.
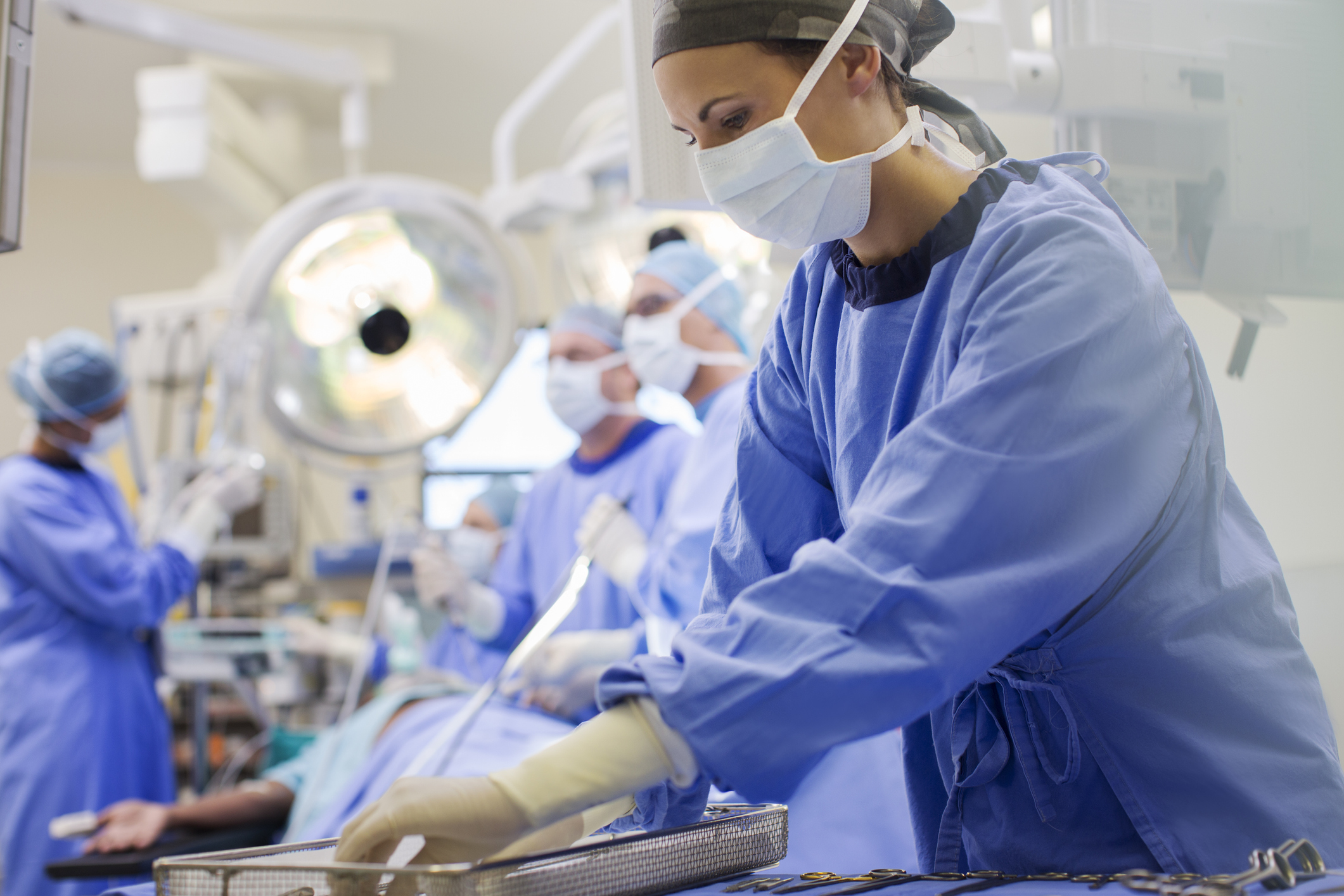
Surgical tools and instruments
As minimally invasive and less invasive surgeries continue to rise, it is important to have tools that are lighter and more ergonomic to prevent surgeon fatigue. These tools must retain the ability of multiple autoclave cycles without degradation of the color, stability, or integrity of the product. Advancements in engineered resins that can withstand autoclaving and some of the harshest cleaning agents provide new opportunities to develop your next surgical tool out of plastic instead of metal. Product experience: biopsy devices, orthopedic devices, women’s health, bezels and housings, and endoscopy.
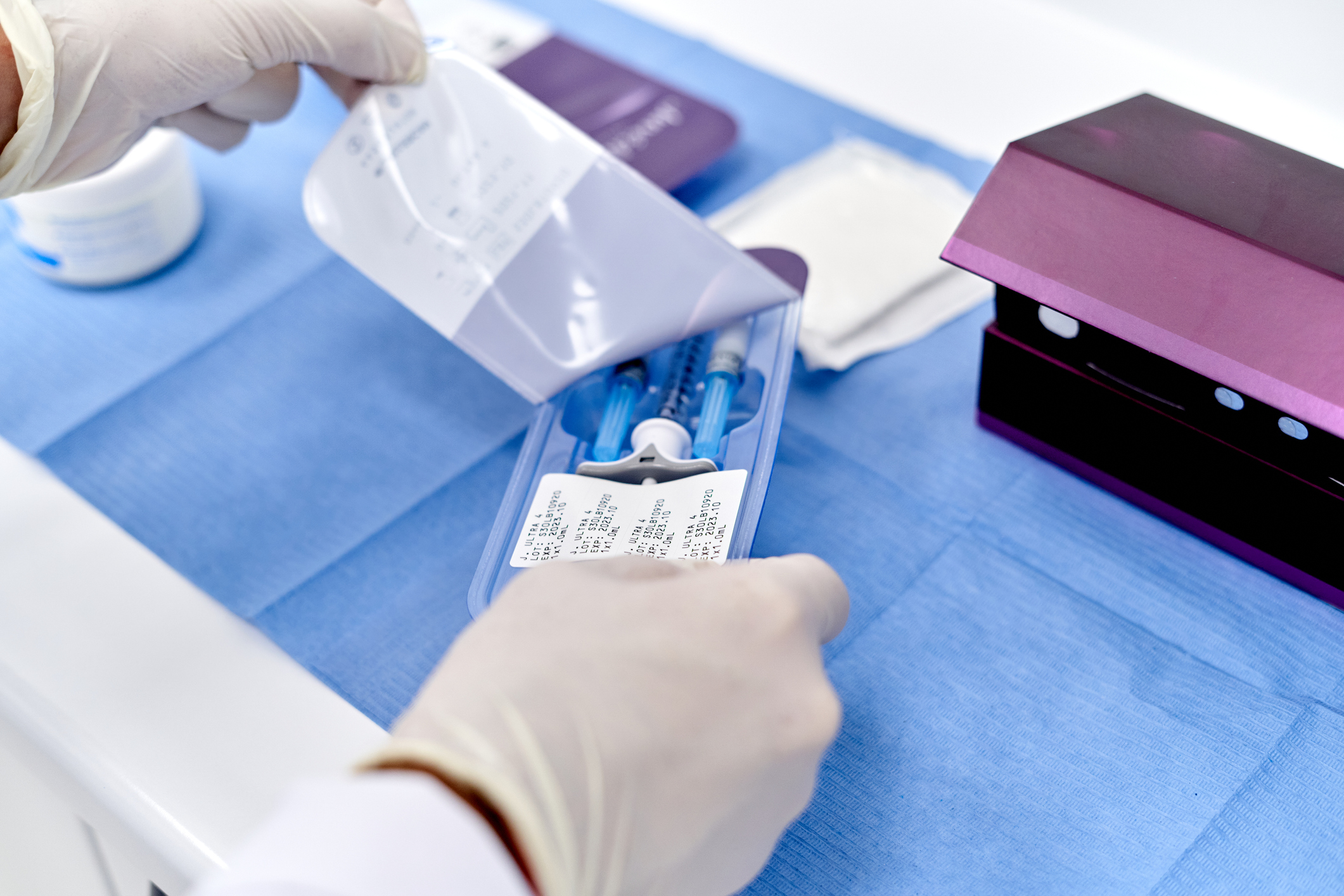
Drug delivery
Vaupell works with numerous drug and liquid handling companies on a variety of projects. These include components and finished goods that are used in DNA sequencing, liquid handling, and microfluidics. Much of this production is developed as RNA/DNA free in our automated manufacturing environment. Our expertise is unsurpassed working with products requiring tight tolerances and using commodity resins. Product experience: Pipettes / trays, Cuvettes, machining of arrays for liquid handling, Chip carriers for microfluidics, Dry-powdered inhalers, Syringe barrels and plungers, and fluid administration sets and winged infusion sets.
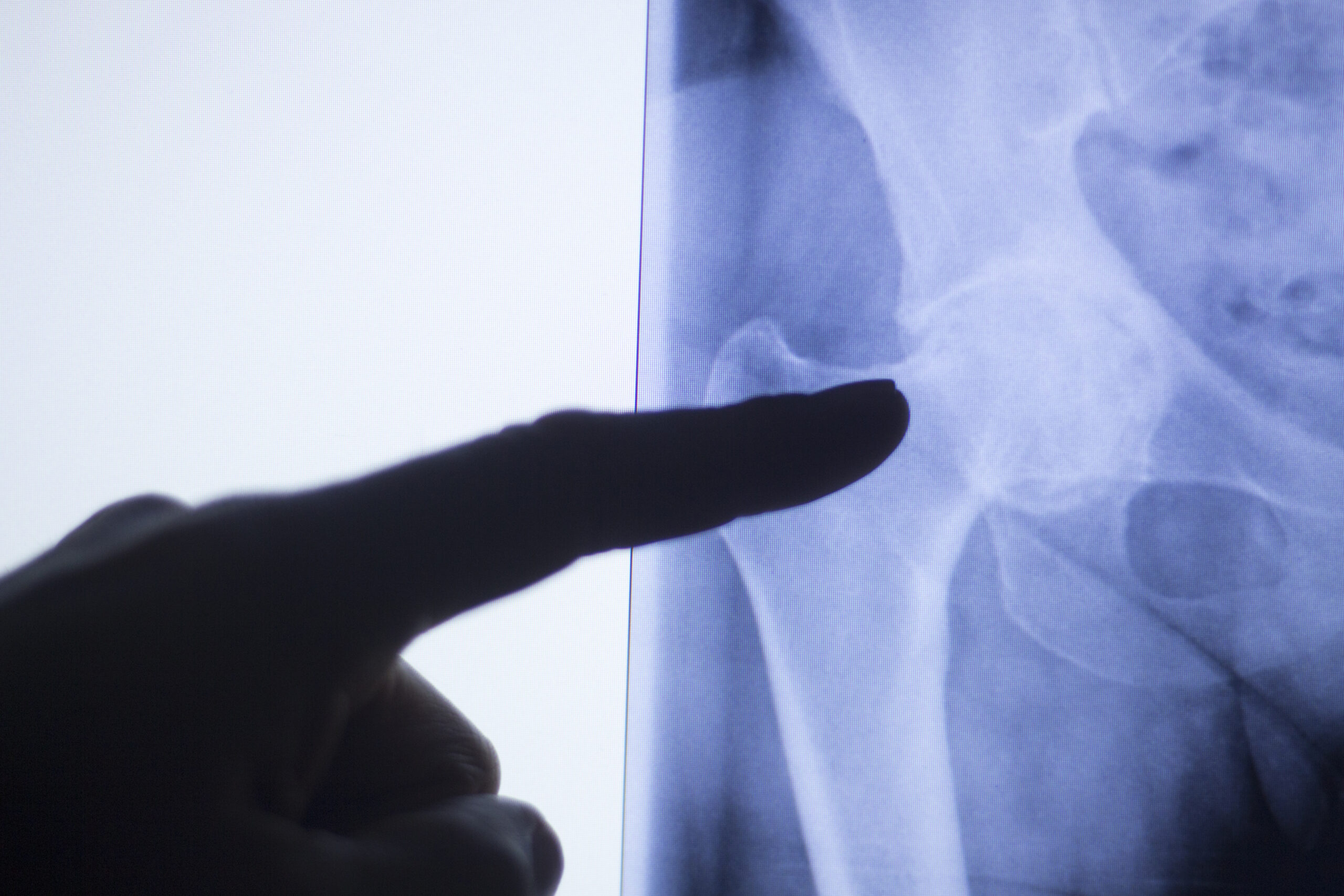
Orthopedics, implantables, & bioabsorables
Vaupell has worked with implant grade and bioabsorbable materials for over 20 years and continues our commitment to this crucial portion of the medical device industry. We control critical properties of these materials through the implementation of Scientific Injection Molding (SIM) processes in Class 7 cleanrooms. Customers work with us to develop short-term and long-term implants. Our team of design, quality, and manufacturing engineers are available to assist in the manufacturability design of these sensitive components. Material experience: PEEK – Optima®, PEEK – Classix®, Endolign®, Bionate® 80A, 90A, PMMA, Purasorb®, PLA, PLLA, PLDL, Resomer®, PLGA – PEG, and Custom Blending.
Concept-to-production
New product introduction, we follow a phase gate approach:
Questions to answer
1. What are the market needs?
2. What concept can meet those needs?
Activities
1. Market research
2. Concept development
Questions to answer
1. Can the product be made?
2. Can a profit be made?
Activities
1. Market research
2. Concept development
Questions to answer
1. What are the design inputs?
2. Does design meet inputs?
3. Does design meet end-user requirements?
Activities
1. Preliminary design & DFM
2. Prototype tooling & build
3. Design verification testing
4. Design validations
Questions to answer
1. What is the rollout plan?
2. What are the critical-to-quality features?
3. What are the risks?
Activities
1. Finalize risk assessment
2. Finalize quality plan
3. Design freeze, ISO/GMP doc’s
4. Production tool build
5. Process validation
Activities
1. Life cycle mgmt.
2. Cont. improvement
Having the right partner makes all the difference
As your trusted partner, we provide comprehensive support and services throughout the entire lifecycle of a product.
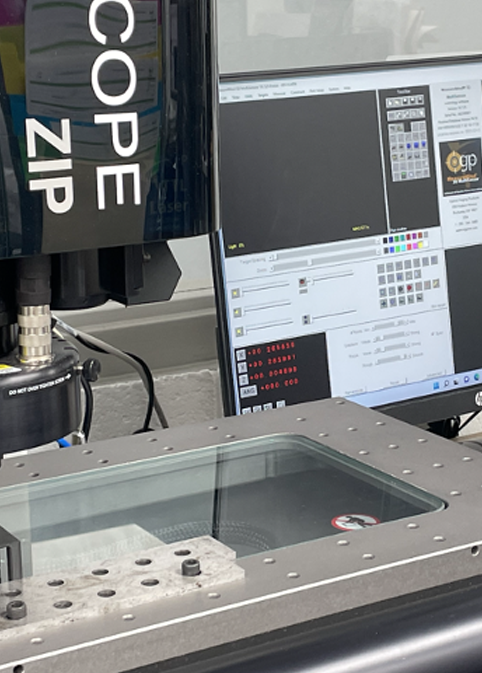
Quality
To ensure consistent quality of the highest level, regular checks are carried out at all process levels and in all production areas by trained personnel using state-of-the-art measurement devices.
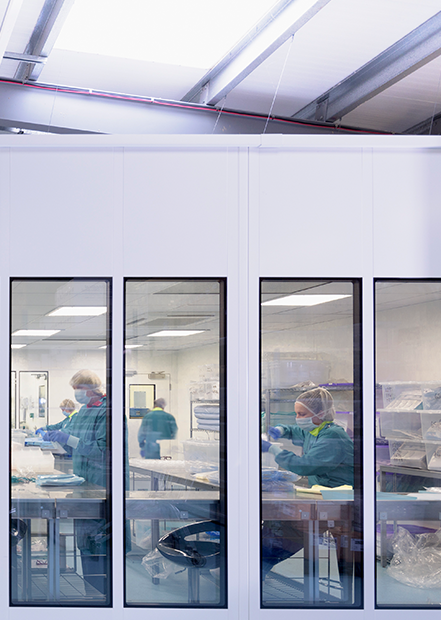
Cleanroom assembly & packaging
Medical cleanroom assembly. We offer precision plastic and metal components with assembly and packaging in a Class 7 cleanroom.
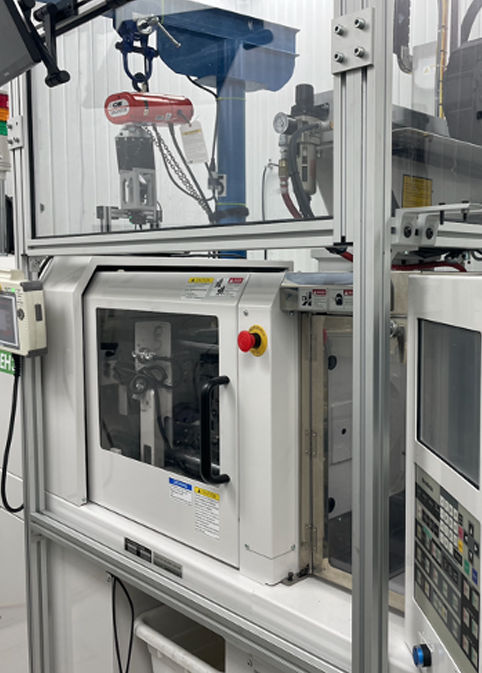
Cleanroom manufacturing
We constantly monitor product quality and have continual cleanroom inspections and requalification by external experts, ensuring the highest possible quality. Our manufacturing takes place in microbiologically controlled Class 7 cleanrooms on cutting-edge, fully automated production lines.
A COMMITMENT TO SUSTAINABILITY
In alignment with parent company Sumitomo Bakelite Co., Ltd., we place a high emphasis on the environment and delivering sustainable solutions.
We solve social issues and achieve sustainable growth and value creation under a structure comprised of our Sustainability Promotion Committee (which is chaired by the President) and its subcommittees based on our business philosophy, which esteems the Sumitomo’s Business Philosophy and sets forth our management principles.
We regularly and comprehensively verify the extent of the progress made by these committees, based on which we continuously revise the contents of our activities and actively improve upon them. In aiming for communication with our stakeholders, we widely announce the results of our activities within and outside the company.
Technologies…
that reduce waste, weight, cost, and manufacturing processes.
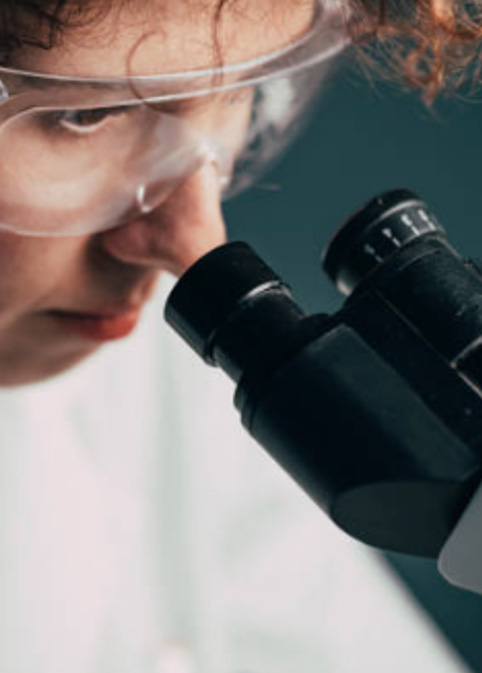
Material science
- Re-using thermoplastic production waste in non-structural products
- PFA replacement of phenolic prepreg and honey comb panels
- Bio-based thermoplastic
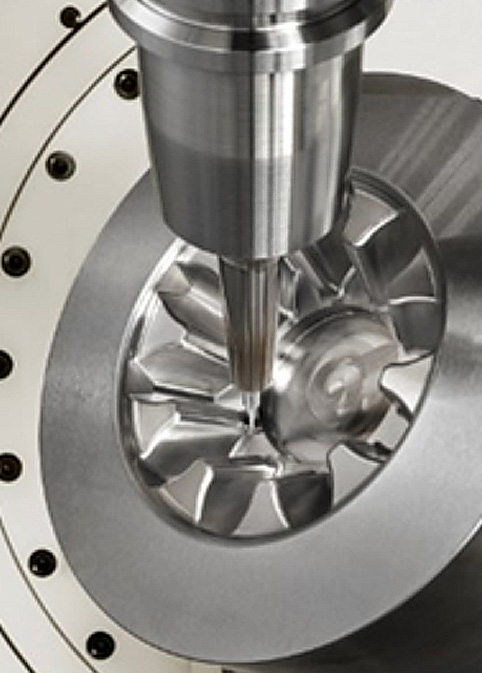
Precision machining
- Milling & turning
- 3 & 5 Axis machining technology
- The choice between 3-axis and 5-axis machining will depend on the specific requirements of your project.
- Parts produced in plastics, aluminum, steels, titanium, composites, and ceramics.
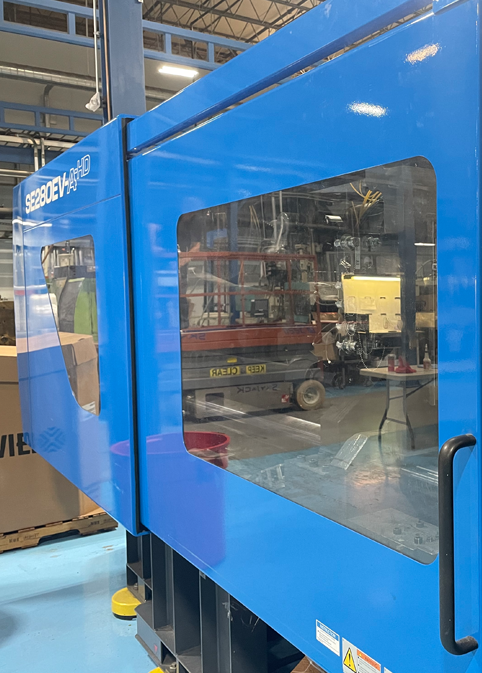
2K injection molding
- Multi-shot molding to eliminate secondary operations & adhesives for bonding secondary components such as seals to panels